Electricity is fundamental to our society. As climate change becomes more severe and demand for clean energy increases, the future is the electrification of everything and along with it, the need for reliable energy. The U.S. infrastructure spans over a vast 200,000 miles and inspecting all of it is a time-consuming and high-risk process that often calls for hanging from helicopters or climbing tall towers. It is inefficient, costly, and dangerous. According to T&D World, utility line work is one of the top 10 most dangerous jobs in America. Around 30 to 50 workers in every 100,000 are killed on the job every year. That’s more than twice the fatality rate of police officers and firefighters.
According to the American Society of Civil Engineers (ASCE), the majority of the nation’s grid is aging, with some components over a century old — far past their 50-year life expectancy — and others, including 70% of transmission and distribution (T&D) lines, are well into the second half of their lifespans. Facing extreme weather events caused by climate change, the U.S.’s aging electric infrastructure in many areas is not equipped to handle volatile conditions – this has played a significant role ranging from destructive summer wildfires in California to deadly winter storms in Texas. Grid outages like these are highly disruptive, expensive, and threaten lives.
One way to address and prevent damage is through routine inspections and maintenance. Utilities have incorporated drones to photograph T&D lines and assets, but have struggled to inspect, analyze and process the images quickly enough to gain precise insights and make proactive maintenance decisions. Conventional inspection methods require manually and subjectively reviewing thousands of images, which can take weeks.
Hitachi Vantara has launched Hitachi Image Based Inspections, an image analytics-based inspection software solution that identifies defects in T&D line assets quickly and accurately. The image-based inspection solution leverages pre-built or custom-built machine learning models to automate defect assessments by instantly processing and analyzing thousands of images in seconds. Hitachi Image Based Inspections replace dangerous, expensive, and time-consuming manual inspections by using the human-in-the-loop approach when required. This results in a significantly faster end-to-end process for image identification, cataloging and health evaluation.
Here’s how it works:
- High-resolution photos of T&D assets are captured by helicopter, ground-based and pole-based photography from multiple angles and are imported for ingestion and preprocessing.
- Hitachi’s AI-based software identifies, inspects, and analyzes the images using machine-learning models and computer vision algorithms to determine defects and failure potential, including information about where the assets are located, for potential equipment defects, such as with insulators or dampers.
- Based on a sample size of 5000 images, on average:
- the model accuracy for assets like dampers, pins, polymer insulators, glass insulators, wooden poles, clamps and copper pins is about 81%.
- the model accuracy for defect detection for items such as bent or damaged dampers, porcelain or ceramic disk damage (such as flashing), insulator or wood pole caps, etc. is approximately 79%.
- Next, we leverage human expertise by bringing in subject matter experts into the analysis loop to validate the AI responses for various conditions including location, defect type, defect severity and time stamp. Over time, the human-in-the-loop inputs create feedback that further trains (or retrains) the AI models to more accurately identify defects.
Hitachi Image Based Inspections generate insights closer to real-time, enabling businesses to make smarter decisions faster, prioritize the most pressing maintenance issues and prevent problems before they can become costly and dangerous. Asset managers can implement a priority-based maintenance strategy to improve reliability, providing operations and maintenance savings. This solution helps increase worker safety, grid reliability and resiliency through more frequent inspections and reduces threat of fire and risk to the public. Plus, Hitachi Image Based Inspections is a fully integrated and scalable solution because it works with existing performance management platforms. Dashboards calculate asset risk scores, predict asset failure, suggest mitigating action, and can create proactive maintenance plans.
Looking beyond power lines, AI-driven automated inspections are a growing class of solutions applicable in any industry where inspections are expensive, high-risk and critical to business continuity such as on-shore or offshore oil rig platforms, wind turbines, hydro dams, utility poles, transformers, cellular towers and antennas, wayside transportation assets, mining and heavy manufacturing equipment, and more. Stay tuned to learn about more use cases in the near future.
Be sure to check out Insights for perspectives on the data-driven world.
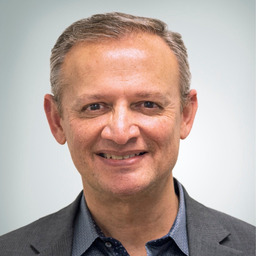
Shamik Mehta
Shamik leads industry solutions marketing for Hitachi Digital Services, with deep expertise in energy, transportation and manufacturing. As well as +25 years working in semiconductors, renewable energy, IoT and data management and analytics.