Manufacturers, from automotive to electronics, recognize the need to evolve their factories into flexible, customer-centric operations. The benefits are too strong to ignore. Once digitally transformed, factories can bring information technology (IT) and operations technology (OT) together to deliver the actionable intelligence they need to improve performance, increase economic returns and respond more quickly to disruptions. But for many original equipment manufacturers (OEMs) and first-tier suppliers, getting there can be challenging.
I know this to be true from first-hand experience. At Hitachi Vantara, we not only work and partner with manufacturers around the globe to digitally transform, but we operate 114 automotive and mobility parts factories ourselves. These factories are microcosms of the industry at large, an industry that is accelerating their transformations with data, analytics, hybrid cloud, AI and automation.
So, we understand the common stumbling blocks manufacturers can encounter along the way, things like knowing how and where to start; identifying what success looks like; and understanding return on investment possibilities.
To help, I’ve outlined four steps that manufacturers can leverage to get started on this journey. These are designed to help operations start to reap benefits from investments and to be better positioned to proactively respond to the ever-changing marketplace.
1. Create a foundation through defined goals, alignment, and leadership support
If you want your Industrial Internet of Things (IIoT) transformation initiatives to be successful, base them on defined business objectives that you can measure through key performance indicators (KPIs) and embrace across your organization. These business drivers will set the parameters for evaluating your success.
In addition, be sure your IIoT initiatives are aligned horizontally within functions, in every facility and region. For example, if you establish a predictive maintenance initiative in one plant, implement that initiative across all your plants and empower a leadership team that looks after that function across all plants. This will help ensure that you are engaging everyone and applying the benefits you gain to the overall success of the business.
Finally, be sure to secure executive leadership support. Leadership sets the tone for adoption across the organization and provides the supporting structure that ensures horizontal alignment and outcomes that are traceable to specific KPIs.
2. Identify opportunities for amplifying benefits
Once you have a keen understanding of your business goals and how you're going to measure success, your next step is to identify use cases where you can apply the power of IIoT to create exponential value for your business. There are hundreds of potential IT/OT use cases in the automotive manufacturing industry, including predictive maintenance, worker safety, energy management, quality and quality traceability, and integrated supply chain. As you define and rationalize these use cases, consider where there might be synergies between them. For example, predictive maintenance initiatives can also lead to improved quality and can enable quality traceability.
After you’ve identified use cases, you can define the logical architecture for supporting them. If you’re applying visualization to your factory, think about how you can use that tool to create a single pane of glass that shows all KPIs across the board in near real time, all in one place. As you define your logical architecture, take into consideration sensor and data-related factors, such as the type of sensing technology you’ll use and how you’ll pull data from those sensors. This is also the time to ensure that you have robust data standardization and normalization, as well as a method for storing that data, such as a data lake. Finally, you’ll need to develop a strategy that determines which use cases will be deployed on the edge and which will be deployed in the cloud.
3. Recognize and drive success through adoption
At Hitachi Vantara, we believe that the No. 1 success criterion for your IIoT transformation journey is organizational adoption. All your other accomplishments will stem from your organization’s readiness and willingness to change the way things get done. To prepare your organization for this journey, you must communicate the value of your transformation to the rest of the organization and discover any skill gaps so you can provide the necessary training to close those gaps.
Organizational readiness is more than recognizing skills gaps, though; it’s a cultural and tactical undertaking from the top down and the bottom up. Strong leadership both champions the change and supplies the resources necessary for driving it to completion — no matter what roadblocks crop up along the way.
4. Embrace the evolutionary nature of ROI
IIoT transformation is a process that unfolds over time, yielding benefits well into the future. Some OEMs initially struggle with how to justify financing this effort. But once they establish the use cases and the criteria for measuring success, they can create a financial model that works for the business — and visualize the benefits they’ll reap from that investment. That’s what we mean by the evolutionary nature of ROI: When you invest wisely up front, your investment can propagate additional benefits that may not even be on your radar yet.
For example, if you deploy a quality control solution that reduces defects and shortens time to market, you can save money and increase revenue. You can then use those funds to drive improvements in other areas, such as energy management, and create exponential value for your organization.
The right investment also leads to proactive operations, as you roll ROI into improving your business when market disruptions occur. Finally, this closer alignment with operations gives operations managers the opportunity for deeper strategic engagement.
Let expert guidance drive your transformation
As you move toward flexible factories of the future by connecting IT and OT, you’ll improve the reliability and availability of your physical assets, minimize the risk of asset failure, and reduce operational costs to achieve a maximum economic return. But most of all, you’ll be able to better predict and respond quickly to the ever-changing dynamics of the market.
Hitachi Vantara has the knowledge and expertise to help. We can help you quickly and easily deploy IIoT transformations that accelerate time to insight and deliver better business outcomes. We do this by leveraging our own proven technologies, advanced analytics and data management capabilities — working in partnership with our clients to co-create solutions that work specifically for their business.
We invite you to reach out to us to discuss how we can help you transform your factory into a flexible, customer-centric factory of the future.
Check out more great stories on Insights.
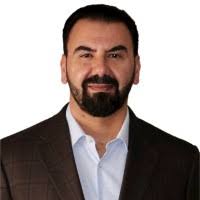
Sa’d Kanan
Sa’d Kanan is Senior Vice President and Global Lead Automotive at Hitachi Vantara.