"Mastering the Fourth Industrial Revolution" was the theme of the 2016 World Economic Forum annual meeting in Davos, Switzerland. The week-long conference was attended by international business executives, investors, government officials, scientists, Nobel laureates, and journalists. The meeting consolidated the latest thinking about digitalization of industry and highlighted the transformative potential of the internet of things, cyber-physical systems, and artificial intelligence. It also legitimized the idea of “smart factories”, where machines, people, and processes are interconnected, augmented by advanced analytics and intelligent algorithms. Suddenly the factory of the future urgently needed to arrive. It was a call to action for industry and governments.
What has happened since then? Over the past 5 years, industrial companies around the world have been seriously investing in digitalization of manufacturing. New budgets for digital transformation have been created. New Digital Manufacturing departments and teams have been established. The topic of digitalizing manufacturing has truly gone mainstream, becoming a featured topic in the annual report of most large and mid-sized industrial companies.
Unfortunately… tangible results over the past 5 years have been mixed. There have been many truly successful breakthrough projects. There have also been many failed projects. Innovation always requires experimentation, with some failures along the way. It is part of the agile method. However, many of the failed smart factory investments can be traced back to flawed strategy and/or poor execution. Most companies are still learning, by doing. What are the key lessons learned, so far?
Hitachi Vantara is supporting hundreds of companies around the world in their smart manufacturing journeys, providing a blend of consulting, technologies, and innovation services. We have worked on projects across a range of sectors, including automotive, aerospace, machinery, electronics, metals, polymers, food & beverage, and packaging. Some of our clients are just starting their smart manufacturing journey, while others are more advanced. Irrespective of the maturity of the company, we have witnessed familiar mistakes being repeated and we have learned many of the critical success factors. Based on these experiences, I will attempt to summarize the top five “lessons learned” in digital transformation of manufacturing.
Lesson 1: Don’t Start with a Solution
Too often, people fall in love with a solution before really understanding the problem(s) to be solved, or the job to be done by the solution. It is like the adage of a hammer looking for nails. A specific technology or a software solution is sometimes pre-selected before fully exploring the needs and constraints of the use case. Solution-centric thinking usually de-rails the innovation process, and very often leads to a failed project. To avoid this pitfall, we encourage our clients to start with an initial analysis and scoping activity which is solution-agnostic. Start with the problem(s) to be solved. Only after the job to be done is well understood, can solution alternatives be explored through. This enables more innovative problem-solving, and potentially better or simpler solutions in the end.
Lesson 2: Go to the Genba
The Japanese word Genba (現場) is defined as the place where value is created. It is where the work is done -- the factory floor. Surprisingly, many companies try to conceive and deploy digital solutions without sufficiently engaging the workforce of the Genba. This inevitably leads to failure. The shop floor staff possess a deep understanding about how production operates today. They also usually have a wealth of ideas about how to make things better. Since they will become the users of the new digital solutions, it is necessary to capture their requirements and preferences when designing the user experience and user interface. And critically, engaging the factory workforce is the best way to gain their acceptance and enthusiasm for the transformation.
Lesson 3: Build Buy-In and Alignment
A global producer of machinery engaged Hitachi to support the digital transformation of a fairly new factory in Europe. Our initial discussions were with their IT director, who had some ideas about what he wanted to do. As we started to meet the factory management team, it became clear that they lacked a shared vision about what they wanted to do, and why. Over the following weeks we helped them to align around a common vision and to align their individual agendas to that vision. Only with the collective buy-in of the key stakeholders, could the project move forward. Building this alignment may sound relatively easy, but surprisingly around 50% of our clients struggle with this. Either they don’t appreciate the importance of it, or internal political gets in the way. Without this alignment, your likelihood of success is quite low.
Lesson 4: Use the Minimum Viable Dataset
One common misconception about digitalizing manufacturing is that you should first build a huge dataset containing all the available data, then start developing algorithms on top. In reality, this approach is backwards -- and usually fails. Best practice is to start with a minimum viable dataset. Select those “critical few” variables that you believe are needed to solve the problem. The “trivial many” variables are best ignored. As the agile development progresses, more variables can be added to the dataset. Sometimes this is based on targeted installation of sensors or cameras. Over time, the dataset can and should grow, adding new variables to your original use case and creating additional use cases. But it is wise to avoid building a massive dataset too early.
Lesson 5: Integrate Digital with Operational Excellence
The purpose of digitalizing the factory is to achieve operational excellence and make a step-change in performance. Your operating system principles, such as 5S, Continuous Flow, JIT Pull System, Theory of Constraints, SMED, Poka-Yoke, Jidoka, SPC, RCA, etc., underpin your manufacturing model. Digitalization is a means to improve these principles through real-time data and advanced intelligence. Unfortunately, many companies still have an Operational Excellence strategy and department which is separated from their Digital strategy and department. Leading companies have joined together these two functions and achieved tremendous results. Yes, your Six Sigma Black Belts are “data scientists”.
In summary, these five practical “lessons learned” should provide you with food for thought. Have you had similar experiences? Should you re-think some aspects of your strategy or execution? In the context of the fourth industrial revolution, five years is not a long time -- so we are all still at the beginning. There are still not always clear right and wrong answers. That’s the nature of innovation. Everyone is learning by doing. You just need to learn faster than your competitors!
About the Author
Greg Kinsey is an Industry Executive at Hitachi Vantara, helping clients to envision, plan, and execute their "Industry 4.0" journeys. With over 35 years of experience in industry, technology, and consulting, he is an international thought leader and trusted advisor in the digital transformation of industry. He began his career as a factory automation engineer at Goodyear, and subsequently led the manufacturing platform business at Digital Equipment Corporation. During the 1990s, Greg was a pioneer in the Lean Six Sigma movement, as Operational Excellence director at both AlliedSignal and Siemens. He went on to executive roles at IBM, HP, Celerant Consulting, and Hitachi.
Greg is a member of the Digital Manufacturing Executive Council at DIGITALEUROPE in Brussels, and a visiting lecturer on Innovation & Design Thinking at Management Center Innsbruck (MCI) in Austria. Greg Kinsey earned his MBA at Georgetown University, and BSc in Mechanical Engineering at Carnegie Mellon University. He is an American-French dual national, residing in Paris.
This story first appeared in Manufacturing Leadership Council’s ML Journal.
Check out more great stories on Insights.
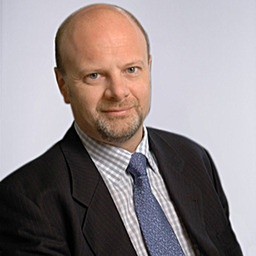
Greg Kinsey
Greg has +35 years' experience in industry, technology and consulting. He began as a factory automation engineer which led to the manufacturing platforms business. He was a pioneer in the Lean Six Sigma movement and held sr. roles at IBM, HP, DEC, AlliedSignal and Siemens.